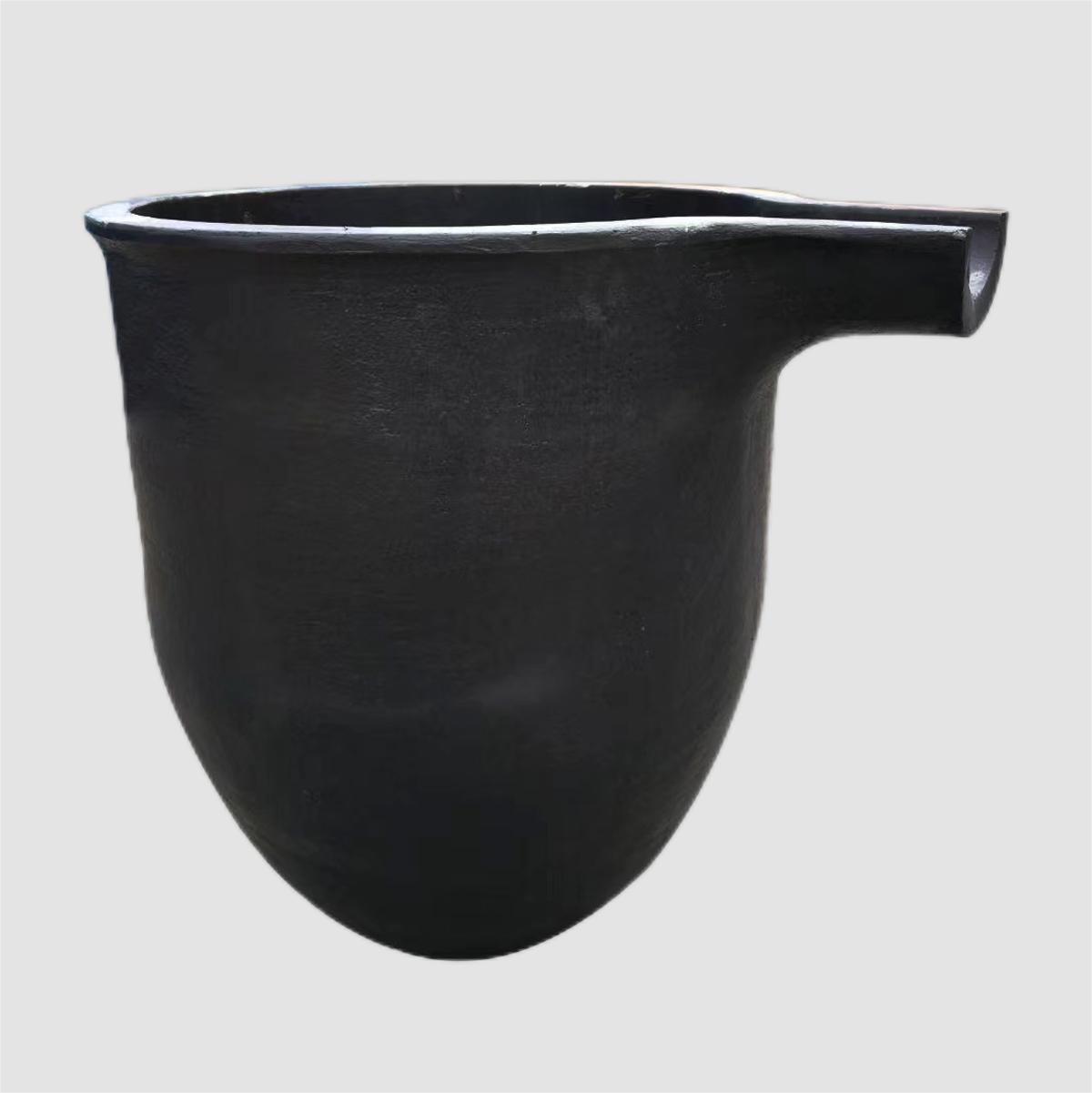
Izostatický lisovaný grafitje nový typ grafitového materiálu vyvinutý v 60. rokoch minulého storočia, ktorý má rad vynikajúcich vlastností.Napríklad izostatický lisovaný grafit má dobrú tepelnú odolnosť.V inertnej atmosfére jeho mechanická pevnosť nielenže neklesá so zvyšovaním teploty, ale sa aj zvyšuje, pričom svoju najvyššiu hodnotu dosahuje pri teplote okolo 2500 ℃;V porovnaní s obyčajným grafitom je jeho štruktúra jemná a hustá a jeho rovnomernosť je dobrá;Koeficient tepelnej rozťažnosti je veľmi nízky a má vynikajúcu odolnosť proti tepelným šokom;izotropný;Silná chemická odolnosť proti korózii, dobrá tepelná a elektrická vodivosť;Má vynikajúce mechanické spracovanie.
Práve pre svoj vynikajúci výkon je izostatický lisovaný grafit široko používaný v oblastiach ako je metalurgia, chémia, elektrotechnický, letecký a atómový energetický priemysel.Navyše s rozvojom vedy a techniky sa oblasti použitia neustále rozširujú.
Proces výroby izostatického lisovania grafitu
Proces výroby izostatického lisovania grafitu je znázornený na obrázku 1. Je zrejmé, že proces výroby izostatického lisovania grafitu je odlišný od procesu výroby grafitových elektród.
Izostatické lisovanie grafitu vyžaduje štruktúrne izotropné suroviny, ktoré je potrebné rozdrviť na jemnejšie prášky.Je potrebné použiť technológiu tvárnenia izostatickým lisovaním za studena a cyklus praženia je veľmi dlhý.Aby sa dosiahla cieľová hustota, sú potrebné viaceré cykly impregnačného praženia a cyklus grafitizácie je oveľa dlhší ako u bežného grafitu.
Ďalším spôsobom výroby grafitu izostatickým lisovaním je použitie mezofázových uhlíkových mikroguľôčok ako surovín.Najprv sa mezofázové uhlíkové mikroguľôčky podrobia oxidačnému stabilizačnému spracovaniu pri vyšších teplotách, po ktorom nasleduje izostatické lisovanie, po ktorom nasleduje ďalšia kalcinácia a grafitizácia.Táto metóda nie je uvedená v tomto článku.
1.1 Suroviny
ThMedzi suroviny na výrobu izostatického lisovaného grafitu patria plnivá a spojivá.Kamenivo sa zvyčajne vyrába z ropného koksu a asfaltového koksu, ako aj mletého asfaltového koksu.Napríklad izostatický grafit série AXF vyrábaný spoločnosťou POCO v Spojených štátoch je vyrobený z mletého asfaltového koksu Gilsontecoke.
Na prispôsobenie výkonu produktu podľa rôznych použití sa ako prísady používajú aj sadze a umelý grafit.Vo všeobecnosti sa ropný koks a asfaltový koks musia pred použitím kalcinovať pri 1200 ~ 1400 ℃, aby sa odstránila vlhkosť a prchavé látky.
Aby sa však zlepšili mechanické vlastnosti a štrukturálna hustota výrobkov, existuje aj priama výroba grafitu izostatickým lisovaním pomocou surovín, ako je koks.Charakteristickým znakom koksovania je, že obsahuje prchavé látky, má samospekacie vlastnosti a expanduje a zmršťuje sa synchrónne so spojivovým koksom.Spojivo zvyčajne používa smolu z uhoľného dechtu a podľa rôznych podmienok zariadenia a požiadaviek na proces každého podniku sa bod mäknutia použitej smoly z uhoľného dechtu pohybuje od 50 ℃ do 250 ℃.
Výkon izostatického lisovania grafitu je výrazne ovplyvnený surovinami a výber surovín je kľúčovým článkom pri výrobe požadovaného konečného produktu.Pred kŕmením je potrebné prísne skontrolovať vlastnosti a jednotnosť surovín.
1.2 Brúsenie
Veľkosť agregátu izostatického lisovaného grafitu je zvyčajne potrebná na dosiahnutie menej ako 20 um.V súčasnosti má najušľachtilejší grafit na izostatické lisovanie maximálny priemer častíc 1 μm.Je veľmi tenký.
Na mletie kameniva na takýto jemný prášok je potrebný ultrajemný drvič.Mletie s priemernou veľkosťou častíc 10-20 μ Prášok m vyžaduje použitie vertikálneho valcového mlyna, s priemernou veľkosťou častíc menšou ako 10 μ Prášok m vyžaduje použitie prúdového mlynčeka.
1.3 Miešanie a miesenie
Rozomletý prášok a uhoľnodechtové smolné spojivo vložte v pomere do ohrievacieho mixéra na miesenie tak, aby vrstva asfaltu rovnomerne priľnula k povrchu častíc práškového koksu.Po vymiesení odstráňte pastu a nechajte ju vychladnúť.
Čas odoslania: 27. septembra 2023